Transforming Management of Tech Assets in Production
Gaining inventory visibility across the production environment.
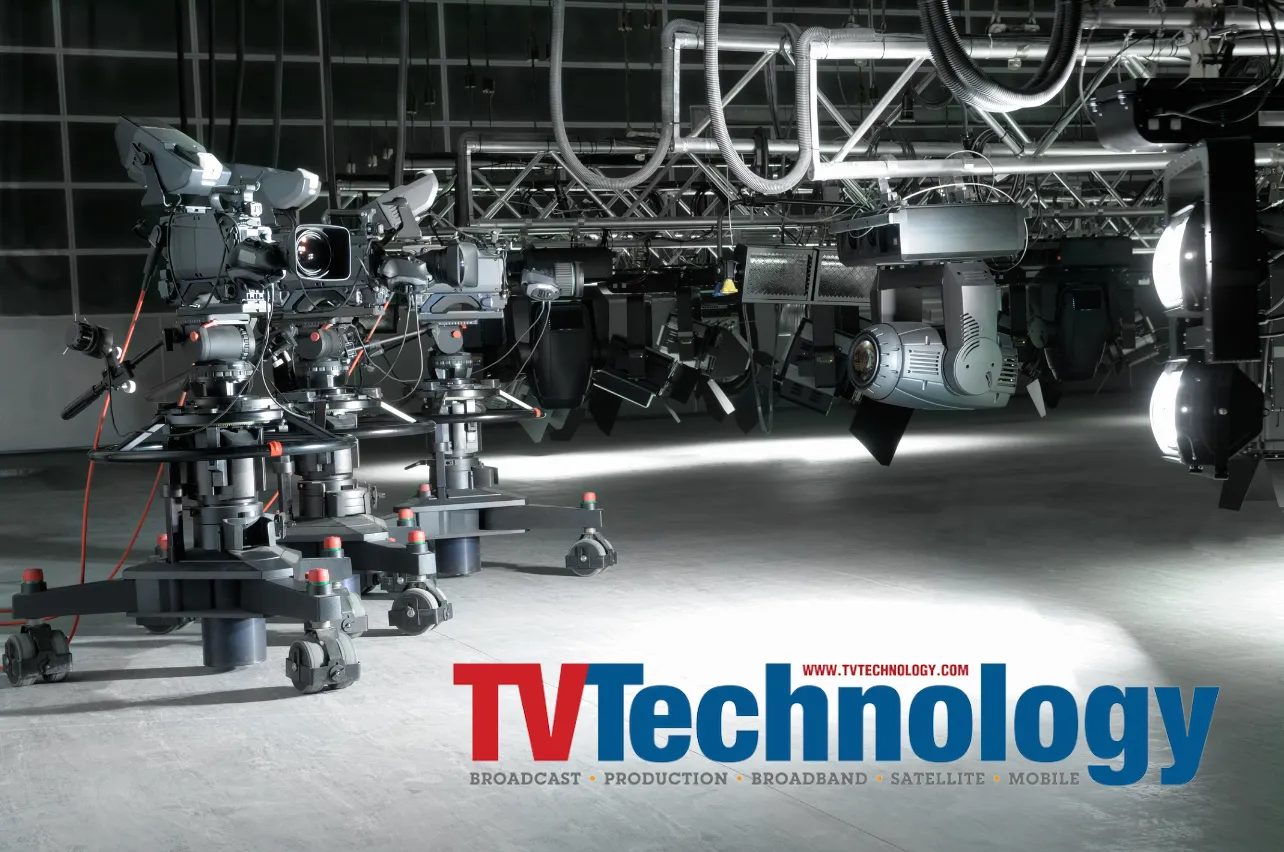
Read the full article at tvtechnology.com
“Finance has SAP. Sales has Salesforce. What do engineers have?”
Kal Hassan, a former vice president of engineering at ABC who has seen countless generations of broadcast equipment come and go, is not the only person asking this question. And he is not alone in recognizing that while most studios, broadcasters, and rental and production companies are embracing smarter, more connected tools and solutions to do their work, few of them capture critical data about their technology inventory. They’ve never had a tool built for that job.
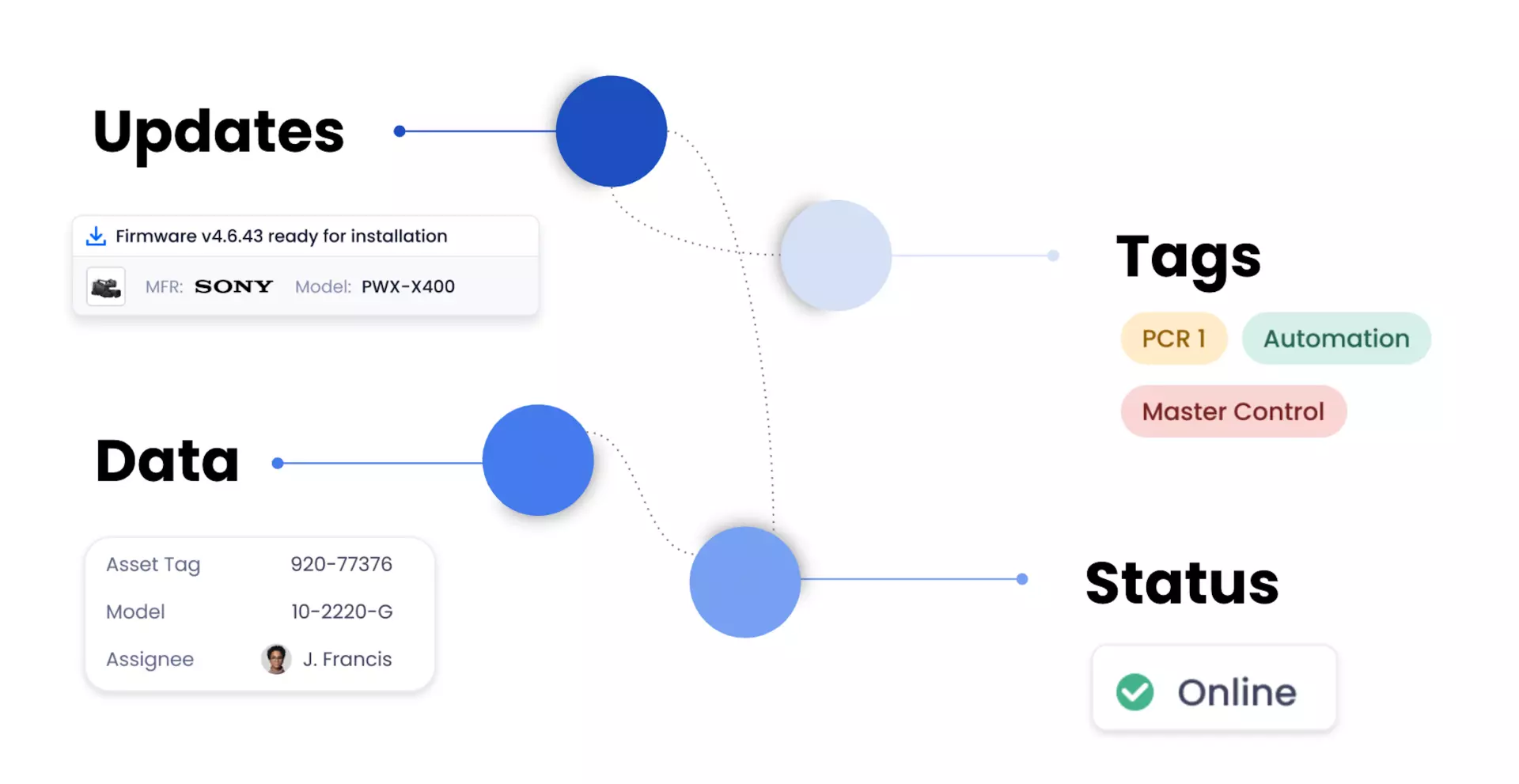
Despite the importance of maintaining uptime and extending equipment life cycles, most media organizations simply rely on an array of spreadsheets to capture asset information in different ways across different documents, often stored in different places. Details frequently are incomplete or out of date. There is no single person or resource an engineer can turn to for reliable — and essential — information about the technology that drives their operations.
“Over the years we tried various different systems to track critical data and updates across all our technology and studio locations but found them all to be lacking in some way,” says Peter Sockett, director of engineering and operations at Capitol Broadcasting.
Media organizations regularly manage 10,000 or more different pieces of hardware, software, and technology to support their production workflows. Across that technology, they work with hundreds of different manufacturers. Without a standardized and centralized tool for storing information about all these systems, locating a vital firmware update, security patch, user manual, troubleshooting guide, or other product-related documents can be difficult and time-consuming, leading to real costs for the business. Product failures, service issues, downtime on set, and preventable security breaches are estimated to cost the broadcasters millions of dollars.
“We visited hundreds of studios and continued to see the same problem on set: engineers were managing thousands of pieces of mission-critical technology with outdated and cobbled-together tools,” says David Kaszycki, CEO, and co-founder of BEAM Dynamics. “Keeping highly complex production workflows operational requires engineers to be on top of firmware, software, and critical security updates, as well as maintain and service hardware and software within those workflows. This currently requires expensive manual labor and individuals to oversee this as an ongoing part of their day-to-day role. When things fall through the cracks, as they often do, it increases vulnerabilities for the workflow and costs over the long run.”
First among those vulnerabilities is a lack of visibility or a lack of awareness of inventory across a facility or group of facilities. Without this visibility, unexpected performance and interoperability issues can arise, and troubleshooting the resulting problems can consume valuable time during a tight production schedule. The solution, says Kaszycki, is to put all the data that engineers need in one place and make it readily available in a common format and user interface, regardless of manufacturer or vendor.
Capturing all of an organization’s inventory assets in a standardized way is a valuable achievement because it gives engineering teams visibility into their entire production inventory across departments and regions. It’s also a crucial first step in improving uptime and reducing costs, particularly for a larger media organization or broadcast group. With access to standardized data about inventory assets across a large broadcast group, for example, the rollout of a software update or server security patch from TV station to TV station suddenly becomes a much simpler, faster proposition.
A second area of vulnerability stemming from a lack of inventory data is the increased potential for product failure. If products aren’t updated, maintained, or replaced as they should be, those oversights can lead to downtime and other issues that can complicate production. If data for each and every product is captured in a standard framework and kept current, engineers can leverage that information to optimize performance (and reduce the risk of a product or workflow failure). They also keep the business in compliance with the latest security standards, in turn minimizing the risk of security breaches and ransomware attacks.
For members of a production team, instant access to current, product-specific information can make all the difference in properly configuring a system or solving a problem. Even if operators are working in the field and have only a mobile device with them, they can quickly locate the documentation or data they need to begin troubleshooting and get back on track. Inventory data can also include the latest shipping guidelines for different regions, product specifications and diagrams, photos, and other details, forms, and paperwork needed to get a replacement product where it needs to be, as quickly as possible.
Robust inventory data can do even more than enhance visibility and, in a variety of ways, help to improve uptime. For an engineer with aging assets, data on important product lifetime events can enable proactive management, support strategic refreshes, and even serve as the equivalent of an ERP system when the time comes to budget for new technology. This data is invaluable for larger organizations, such as broadcast groups and rental houses, that grow through acquisitions and need a way of visualizing the inventory of their newly extended operations. With a standardized and centralized system for managing and dynamically maintaining product data, they can be proactive and strategic from the start in how they own, manage, and deploy those resources.
Media organizations are just now beginning to gather and understand operational data — how productions operate, how technology is managed on set, where there are issues with equipment, and how those issues might cause downtime and delays in production — with the aim of improving their efficiency, reducing costs, and boosting uptime.
The benefits are clearer than ever, but two fundamental challenges remain: aggregating and maintaining inventory data. Hassan is quick to point out that the process of collecting data is an immense undertaking requiring a great deal of manual labor. He suggests, however, that some of the information needed to fill out a database may already exist in unexpected places. The finance department, for example, may maintain product lists in order to track depreciation for tax purposes.
Maintaining current information is likewise a significant challenge and a never-ending process. Over the course of every product’s lifetime, there may be firmware updates, additional documentation, and other resources released to help keep that asset performing at its best. With the introduction of technology management platforms, such as BeamON from BEAM Dynamics, to the broadcast market, engineers finally have a modern tool for connecting their asset inventory with every data element related to it. Requiring only the model number and manufacturer for each piece of technology, this new breed of management platform can automatically connect asset inventory lists to a rich set of data, updates, documents, and resources directly from OEMs.
As a result, engineers and production team members can maintain access to all critical security patches, firmware updates, documentation, and contact information for thousands of vendors and hundreds of thousands of products, all in one web-based user interface. In the future, as this technology evolves, broadcasters can expect to see cutting-edge data science and modern tools such as machine learning and artificial intelligence applied to deliver further capabilities and benefits.
“As technology management platforms are deployed across different studios and production environments, the technology will grow in intelligence about how technology assets are owned and managed,” notes Hassan. “With more and more data on product usage and common issues, complemented by AI-driven analysis, this technology will evolve into an even more powerful tool, with valuable predictive capabilities around downtime and potential issues.”
Other articles
Learn more about technology management, industry tips, product news and more.